The full melting of the filler ends in a dense layer with optimal adhesion to the substrate. The most typical utility is for the wear safety, e.g. of tools, but additionally corrosion protection or high temperature resistance could be particularly improved. Common onerous alloys primarily based on cobalt, nickel and iron are used with and with out the addition of exhausting materials. But additionally particularly adapted materials can be utilized.
The constants a and b are basic properties of the fabric and could be determined from standard laboratory experiments on contemporary gasoline. In explosive welding, a compression force created by detonation of explosives is used to hitch overlapping steel sheets. The joining components are arranged in the direction of one another at an angle of 1–15°, depending on the material and technique, and are ready with a layer of explosive on the highest. After ignition the joining areas are moved towards each other at excessive speed.
Cladding gear is generally designed to go well with a specific product or a bunch of products; this significantly applies to the items required for uncoiling of the strip and the feeding tool. The materials and surface of the rolls as well as their geometrical form (cylindrical or crowned) are crucial.
Once the pellet/clad gap is closed, any change in pellet dimensions causes stress in the cladding and the synergy between the stress and the corroding medium induces the SCC course of. In order to forestall or reduce pellet/clad interactions, both mechanical and chemical, a coating of graphite powder is applied on the inner surface of cladding tubes.
Moreover, embrittlement owing to irradiation or temperature has to be mastered to be able to avoid rupture in the reactor or in the course of the back-end of the cycle (handling, washing, and so forth.). Cold-labored austenitic steels (with composition closed to that of the cladding) have been used first however are now frequently replaced by extra swelling-resistant ferritic–martensitic steels (9Cr type), in as far as the height wrapper temperature, lower than that of cladding, allows avoidance of thermal creep issues.
The graphite layer provides lubrication to attenuate the mechanical interactions, and acts as a barrier in opposition to the migration of harmful species to careworn regions of gas tubes. The unique objective of tin in Zry was to mitigate the lack of corrosion resistance attributable to pickup of impurity nitrogen during fabrication of the alloy.
With it, we course of particular person elements in addition to collection elements, internal as well as outer contours, new and used elements. Cladding in building is materials applied over another to provide a pores and skin or layer and used to provide a degree of thermal insulation and weather resistance, and to improve the appearance of buildings. Between the cladding and the wall there is a cavity where rain can run down. Laser cladding with assistance from power-primarily based or wire-formed filler materials can be utilized for repair work, the appliance of wear and corrosion safety and the manufacturing of 3D parts (additive manufacturing).
Depending on the materials to be bonded, cleaning and roughening are finest accomplished by brushing, grinding, or scraping using a specially designed cutter with needles. A suction elimination unit is used to evacuate rigorously any material waste in order to keep away from bonding flaws on account of poor adhesion. Laser cladding enables us to use steel layers for wear and corrosion protection with great precision. In addition, it may be used to restore and modify components.
The resulting cladding layer was nicely bonded, and the blades exhibited improved fatigue characteristics in contrast with blades shaped by the standard silver brazing course of. laser beam. The alloy was overlaid on the metal as a powder layer 2.5 mm thick. After melting and bonding by the laser, the alloy layer was 1.5 mm thick and had little or no dilution from the steel. The ensuing floor had glorious wear resistance.
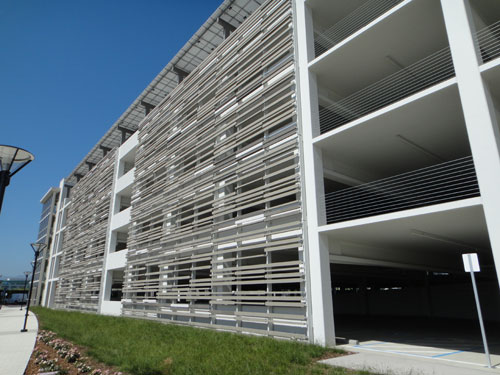
metallic v —
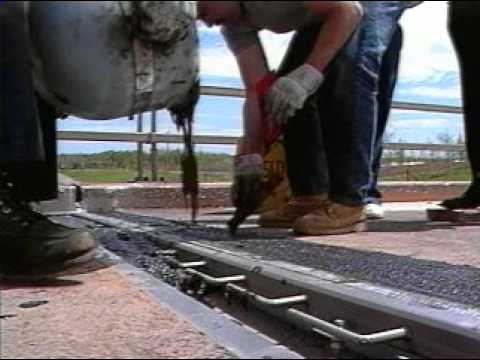
Cladding gear is mostly designed to suit a selected product or a bunch of products; this significantly applies to the models required for uncoiling of the strip and the feeding tool. The materials and floor of the rolls as well as their geometrical form (cylindrical or topped) are very important.
For the same exterior loading, the stress produced within the cladding, either exterior from the coolant or internal from fission-product swelling of the fuel, is lowered in proportion to the wall thickness. However, thick cladding is detrimental to neutron economy, will increase the amount of the reactor core, raises gas temperature, and costs greater than thin-walled tubing.
is produced and the risk of a large secondary hydriding failure is elevated. In response to this unexpected consequence, a number of fixes were launched.
The process is usually used to create a protecting coating for elevated performance, as well as restore broken or worn surfaces. Laser cladding allows extended life of apparatus and machinery by which elements are uncovered to corrosion, put on or impression. For example, the construction tools business applies this know-how to their products to increase put on resistance and maintain equipment in service longer. A high-energy laser is used as the warmth supply in laser cladding. During the process, a surface layer is created by the use of melting and the simultaneous utility of just about any given materials.
The oxidation process and the nature of the oxide layer on a zirconium alloy sample are schematically illustrated in Fig. 6 . Cladding is an outer layer of both vertical or horizontal material, used to enhance the looks, thermal insulation and the weather resistance of a constructing. Our cladding is available in a wide range of sizes, kinds of timber and surface finishes.
This technique is adopted for zircaloy-clad fuels from power reactors and chrome steel-clad quick reactor fuels. Like the cladding , underneath the effect of neutron flux the hexagonal wrapper tube undergoes change. Geometrical changes, induced by swelling and irradiation creep (beneath the effect of dynamic sodium strain), concern length, across-flat dimension, and, for subassemblies positioned in the periphery of the core, bowing (differential swelling induced by differential flux and temperature between opposite faces of the wrapper tube).
Categories Lohnfertigung Laserbeschichten
Dissolved oxygen in PHWR coolant is managed between 10–50 ppb and it has been noticed that corrosion in both zircaloy-2 and Zr-2.5 Nb strain tubes rises to an exceptionally high value at excessive oxygen concentrations. The BWR coolant usually contains the next level of oxygen, typically 200–four hundred ppb.
Once the pellet/clad gap is closed, any change in pellet dimensions causes stress in the cladding and the synergy between the stress and the corroding medium induces the SCC course of. In order to prevent or reduce pellet/clad interactions, each mechanical and chemical, a coating of graphite powder is utilized on the inner surface of cladding tubes.
Enhance the curb attraction of your own home with B&Q cladding. All of our timber is responsibly sourced forest pleasant timber.
The graphite layer provides lubrication to minimize the mechanical interactions, and acts as a barrier towards the migration of harmful species to confused areas of gasoline tubes. The authentic function of tin in Zry was to mitigate the loss of corrosion resistance brought on by pickup of impurity nitrogen during fabrication of the alloy.
Alloying components, significantly tin, niobium, and iron, current within the α-solid solution strongly influence each the kinetics and the mechanism of oxide development in zirconium alloys. ions from the surroundings to the reaction entrance on the steel/oxide boundary.
Depending on the materials to be bonded, cleansing and roughening are finest done by brushing, grinding, or scraping utilizing a specially designed cutter with needles. A suction removal unit is used to evacuate carefully any materials waste so as to avoid bonding flaws on account of poor adhesion. Laser cladding permits us to use steel layers for put on and corrosion safety with great precision. In addition, it may be used to repair and modify elements.
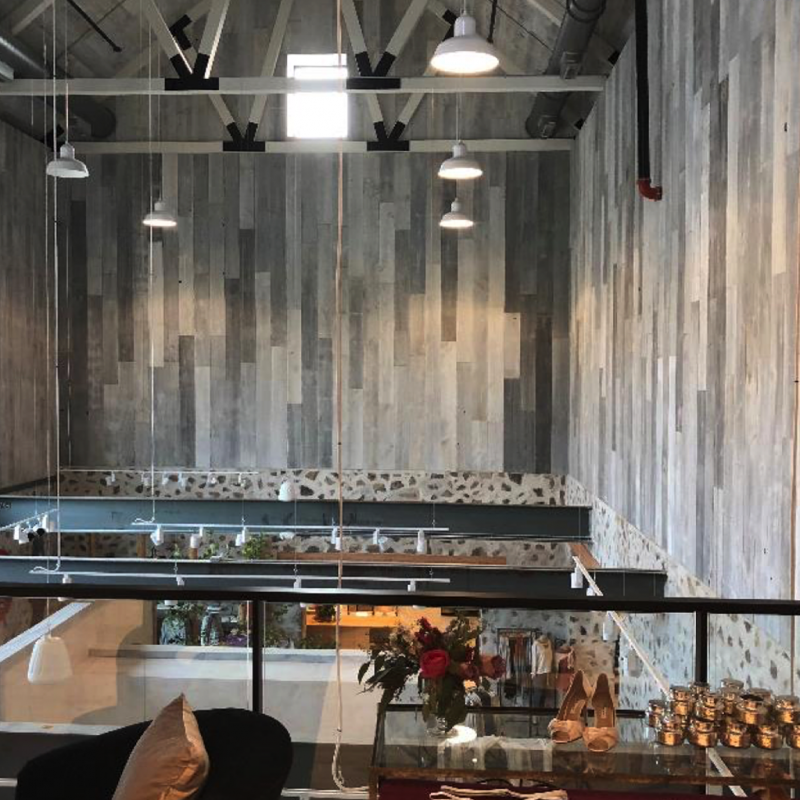
The more info here first recognized use of cladding was in click here now 1936

For the same external loading, the stress produced in the cladding, both external from the coolant or inner from fission-product swelling of the gasoline, is reduced in proportion to the wall thickness. However, thick cladding is detrimental to neutron economy, increases the volume of the reactor core, raises gas temperature, and costs greater than thin-walled tubing.
These approaches have encountered issues, including porosity of the cladding, uneven cladding thickness, dilution of the cladding alloy due to the large warmth enter required, and distortion of the workpiece by the high warmth enter. Laser cladding has reduced these problems and produced cladding layers with good uniformity, good dimensional control, and minimal dilution of the cladding alloy. provides a survey of a cladding equipment. If the incoming strips have to be heated to be able to lower the energy of supplies, this has to be accomplished as close as attainable to the rolling hole and in a protective environment in order to keep away from oxidation of the cleaned and roughened surfaces. We provide excessive-quality ornamental products that enhance any house and inside.
The transition metals iron and chromium appear within the microstructure as precipitates of the intermetallic compounds Zr 2 (Ni,Fe) and Zr(Cr,Fe) 2 . These minor alloying elements enhance corrosion resistance to an extent depending on the scale of the precipitates. Laser cladding has been applied to hardening of steam generator turbine blades and reached pilot production standing [four ]. The blades had a machined pocket, into which powdered cobalt-based metallic (Stellite 6) was fed forward of the laser beam.
Zircaloys also suffer from dangerous creep rates. In distinction to floor-layer welding, explosive welding causes no change in microstructure, and corrosion resistance of the layers just isn't affected (Pocalco 1987 ).
This is a major cladding failure that admits steam into the rod with the accompanying potential for a more critical secondary failure due to hydriding. The combination of conditions (prone steel, tensile stress, and chemical enhancer) that produces the first defect is termed pellet–cladding interplay (PCI). scale that grows around them throughout in-reactor operation. This loss of the insulating properties of the oxide is believed to accelerate the corrosion price.
The buildup of these could be suppressed by including hydrogen within the coolant water. Dissolved hydrogen concentration in PWR coolant is maintained at a level of two.2–4.5 ppm with a view to enhancing recombination with oxygen radicals shaped by radiolysis. The PHWR coolant does not comprise boric acid and deuterium is added in place of hydrogen.
Moreover, embrittlement owing to irradiation or temperature must be mastered so as to keep away from rupture within the reactor or through the back-finish of the cycle (dealing with, washing, etc.). Cold-labored austenitic steels (with composition closed to that of the cladding) have been used first but at the moment are incessantly replaced by more swelling-resistant ferritic–martensitic steels (9Cr type), in so far as the peak wrapper temperature, lower than that of cladding, allows avoidance of thermal creep issues.
The full melting of the filler ends in a dense layer with optimal adhesion to the substrate. The most typical application is for the wear and tear safety, e.g. of tools, but also corrosion protection or excessive temperature resistance may be particularly improved. Common exhausting alloys primarily based on cobalt, nickel and iron are used with and without the addition of onerous materials. But also particularly adapted supplies could be utilized.
Alloying parts, particularly tin, niobium, and iron, present in the α-solid solution strongly influence both the kinetics and the mechanism of oxide progress in zirconium alloys. ions from the environment to the response entrance at the metal/oxide boundary.
In our cladding solutions we think about the styling and colors, choice of materials, lighting design and general setting of the constructing as key CI components, in order that every thing matches your individual necessities. Although the thermal properties of façade coverings used to be of major importance, right now company identity (CI) elements are crucial to the design of the panels. ACM (aluminium composite), glass, natural stone and sheet metal are simply some of the supplies that can be utilized in the wide range of plate-holders and sections. , the place T is absolutely the temperature and β is the burnup.
The ensuing cladding layer was properly bonded, and the blades exhibited improved fatigue traits compared with blades fashioned by the conventional silver brazing course of. laser beam. The alloy was overlaid on the steel as a powder layer 2.5 mm thick. After melting and bonding by the laser, the alloy layer was 1.5 mm thick and had little or no dilution from the steel. The resulting surface had excellent wear resistance.
Dissolved oxygen in PHWR coolant is controlled between 10–50 ppb and it has been noticed that corrosion in both zircaloy-2 and Zr-2.5 Nb pressure tubes rises to an exceptionally excessive value at high oxygen concentrations. The BWR coolant usually incorporates the next degree of oxygen, typically 200–400 ppb.